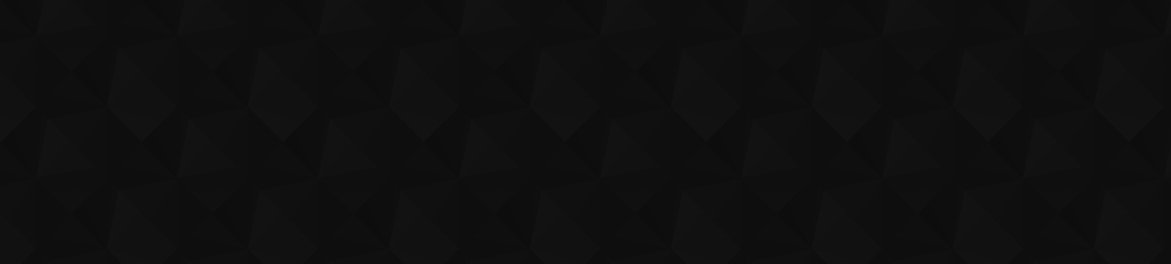
- 115
- 480 480
RJG, Inc.
United States
Приєднався 8 лип 2009
Since 1985, RJG has been delivering customer success through their deep passion and knowledge of all aspects of the plastic injection molding process. This allows customers to achieve unmatched financial success through a unique combination of consulting, training, and technology. In all they do, RJG strives to empower the plastics industry to create positive change in the world.
An Overview of MAX, CoPilot, and The Hub
Here’s a brief overview of MAX, CoPilot, and The Hub for injection molding process control and networking.
About MAX: Molding Automation Xperience, or MAX for short, features an intuitive and easy-to-use interface that provides step-by-step advice to help you restore your process to optimal performance. This smart AI, powered by proven Master Molder® techniques, delivers you with an unparalleled level of control, efficiency, and quality never before possible.
rjginc.com/copilot-process-control/
About CoPilot: CoPilot is the industry’s latest injection molding process control system, equipped with all of the benefits of traditional systems that we’ve all come to know and trust with the added bonus of an extremely user-friendly interface and an AI-powered advisor. This system packs in all of RJG’s vast amounts of knowledge and experience into a tiny box, which now provides real-time advice to get you back to making good parts again fast. The best part? It’s so easy, people with any experience level can now fix a process!
rjginc.com/copilot/
About The Hub: The Hub is a plant-wide networking system that makes it easier than ever to keep your production floor on track. Get global facilities on the same page with standardized processes, automated audit reports, data-driven decision making, machine databases, and much more.
rjginc.com/the-hub/
#moldsmart #injectionmolding #plastic #technology #rjg #processcontrol
About MAX: Molding Automation Xperience, or MAX for short, features an intuitive and easy-to-use interface that provides step-by-step advice to help you restore your process to optimal performance. This smart AI, powered by proven Master Molder® techniques, delivers you with an unparalleled level of control, efficiency, and quality never before possible.
rjginc.com/copilot-process-control/
About CoPilot: CoPilot is the industry’s latest injection molding process control system, equipped with all of the benefits of traditional systems that we’ve all come to know and trust with the added bonus of an extremely user-friendly interface and an AI-powered advisor. This system packs in all of RJG’s vast amounts of knowledge and experience into a tiny box, which now provides real-time advice to get you back to making good parts again fast. The best part? It’s so easy, people with any experience level can now fix a process!
rjginc.com/copilot/
About The Hub: The Hub is a plant-wide networking system that makes it easier than ever to keep your production floor on track. Get global facilities on the same page with standardized processes, automated audit reports, data-driven decision making, machine databases, and much more.
rjginc.com/the-hub/
#moldsmart #injectionmolding #plastic #technology #rjg #processcontrol
Переглядів: 132
Відео
Congratulations on your retirement, eDART!
Переглядів 7482 місяці тому
Join us in celebrating the eDART as it prepares to enter its retirement in May 2025 after 20 years of serving the injection molding industry. eDART was the first of its kind and has shifted the injection molding standard across the globe, helping molders become more efficient and cost effective than ever before. Though it's a bit bittersweet saying goodbye, we're excited to pass the torch onto ...
Introducing MAX - The Injection Molding Industry's First AI Process Control
Переглядів 28 тис.6 місяців тому
Meet MAX, the industry's first AI-powered process control system, available NOW on CoPilot!!! MAX will walk you through step-by-step how to fix a process, no matter your experience level, so you can make good parts again fast! It's time to harness the power of AI to bridge the skills gap, improve profitability, and reduce downtime. Start here: zurl.co/rOKz #injectionmolding #AI #artificialintel...
A Brief Demo of MAX, the Process Advisor
Переглядів 9646 місяців тому
Here is a brief demo of our latest innovation: MAX, the Process Advisor. MAX is a step-by-step guide that utilizes proven Master Molder techniques to help molders fix injection molding processes regardless of their experience level. Find out more: rjginc.com/copilot-process-control/ #injectionmolding #plastic #technology #processcontrol #RJG #moldsmart
8 second savings RJG testimonial .mp4
Переглядів 44611 місяців тому
Want to learn just how much 8 seconds can save you? request a consultation today: zurl.co/2ZoA
Part & Mold Design Course.mp4
Переглядів 463Рік тому
🌟 NEW COURSE ANNOUNCEMENT! 🎉 Join us at @Rowan-Cabarrus Community College October 3rd for this game changing course where you will learn the common language and universal knowledge required to design and produce #plastic injection molds and molded components. Register today: zurl.co/CggB #training #injectionmolding #molddesign
5 Reasons to Try Injection Molding eLearning
Переглядів 628Рік тому
eLearning has become increasingly popular in recent years, with more and more individuals and organizations turning to virtual injection molding training options as a viable alternative to traditional classroom-based training. Here are 5 reasons why. #InjectionMolding #RJG #RJGAcademy #MoldSmart #Training #elearning #Plastic
A Look into Math for Molders eLearning
Переглядів 1,8 тис.Рік тому
Wondering what an eLearning course from RJG looks like? Here's a sneak peek inside Math for Molders eLearning. Learn more and register here: rjginc.com/training/registration/math-for-molders-elearning/ #injectionmolding #training #elearning #moldsmart #RJG #RJGacademy
A Look into Introduction to Material Handling eLearning
Переглядів 660Рік тому
Wondering what an eLearning course from RJG looks like? Here's a sneak peek inside Introduction to Material Handling eLearning. Learn more and register here: rjginc.com/training/registration/material-handling-elearning/ #injectionmolding #training #elearning #moldsmart #RJG #RJGacademy
A Look into Essentials of Injection Molding eLearning
Переглядів 1,6 тис.Рік тому
Wondering what an eLearning course from RJG looks like? Here's a sneak peek inside Essentials of Injection Molding eLearning. Learn more and register here: rjginc.com/training/registration/essentials-of-injection-molding/ #injectionmolding #training #elearning #moldsmart #RJG #RJGacademy
Why Cooling is Vital in Medical Injection Molding and How to Perfect It
Переглядів 16 тис.Рік тому
Cooling is an absolutely vital (and often overlooked) part of the injection molding process, especially in the medical industry. Cooling greatly affects dimensions, which is a huge deal when it comes to safety critical parts with extremely tight tolerances. In this webinar host by MAPP, Cory discusses why cooling efficiency is so important and gives valuable tips on how to master it that you ca...
Shrinkage Effects on Various Materials, Additives, and Processes in Injection Molding
Переглядів 4,4 тис.Рік тому
Shrinkage can have different effects on injection molded parts depending on the type of materials and additives used and the processing strategy put into place. Here's an overview of some of those effects. #moldsmart #rjg #injectionmolding #materials #plastic #processing #howto
Webinar: The Difference Between Hydraulic, Specific, and Cavity Pressures
Переглядів 3,5 тис.Рік тому
Jason Robinson presents a webinar through MAPP (Manufacturing Association for Plastics Processors) explaining the three different types of pressures: hydraulic, specific, and cavity. Each one of these holds a unique and very important role in the injection molding process. #moldsmart #rjg #howto #injectionmolding #plastic
What Is Back Pressure in Injection Molding?
Переглядів 29 тис.Рік тому
RJG expert Trainer / Consultant, Jason Robinson, talks about the importance of back pressure in injection molding and how to use it to make better plastic injection molded parts. Read more about back pressure on our blog: rjginc.com/what-is-back-pressure-in-injection-molding-why-is-it-important/ #moldsmart #injectionmolding #materials #plastic #resin #systematicmolding #howto
Semi-Crystalline vs Amorphous Materials
Переглядів 4,6 тис.Рік тому
Semi-Crystalline vs Amorphous Materials
4 Ways the CoPilot Can Help You Reduce Costs
Переглядів 1,5 тис.2 роки тому
4 Ways the CoPilot Can Help You Reduce Costs
How to Clean an Injection Mold Inside the Machine
Переглядів 13 тис.2 роки тому
How to Clean an Injection Mold Inside the Machine
Injection Molding and Design Expo Speaker Spotlight
Переглядів 3482 роки тому
Injection Molding and Design Expo Speaker Spotlight
Inside the Walls of RJG: Come Work with Us
Переглядів 4822 роки тому
Inside the Walls of RJG: Come Work with Us
Learn More About the CoPilot Injection Molding Process Control Software
Переглядів 1 тис.2 роки тому
Learn More About the CoPilot Injection Molding Process Control Software
Moldex3D Presentation: Enhancing Prediction Accuracy via Sensor Technologies
Переглядів 9132 роки тому
Moldex3D Presentation: Enhancing Prediction Accuracy via Sensor Technologies
Révélation du logo : Bienvenue dans le nouveau visage de RJG
Переглядів 2192 роки тому
Révélation du logo : Bienvenue dans le nouveau visage de RJG
Logo Revelado: Bienvenido a la Nueva Cara de RJG
Переглядів 1862 роки тому
Logo Revelado: Bienvenido a la Nueva Cara de RJG
they're great!
😊
interesting! what's the difference between specific and back pressure?
Video is very helpful, thanks. I have a question though, Duponts nylon guide says to use the maximum pressure for the holding stage. This bottoms out the screw though. Or if I increase the shot size too far I get flash. Should I not use such a high pressure?
Another thing i have seen is guys increase the shot size when the shit goes short and i have to fix the fucking nozzle leak plastic everywhere!
Flash could be caused by a lot. Over venting the mold, big shot size, barrel heates too high, or mold damage/tool damage. Shorts are usually just not a big enough shot but usually if you are short on one side and flasing on the other there is a problem with the mold or how the press is leveled.
You forgot the real reason for Back Pressure - air will travel to the area of least resistance - no bp - air goes to the front of the screw
Clamp tonnage not set right and mold cooling working correctly will cause flash....now is the die-height set correctly is your lockup position correct. Do you have a broken tie-bar and is the mold there damage causing the flash?
Please make a detailed video that how a molding machine works …like each step …injection pressure ,injection speed ,injection position in barrel ,screw recovery back pressure suck back
That's a great idea!! We'll add it to our list. Thanks!! 😁
Sir u mean we should fill the part by using two profiles?
Poly is easy to mold. Try 14 inch cpvc sch 80 tees 😅.
Sad times, I will miss the edart
It's bittersweet for sure... We're excited for the future, though!
excellent explanation, thank you
We're so glad you enjoyed it! Thanks for watching!
thank you for your presentation. I would like to ask you, what do you recommend to use instead of safety couplings?
why dont you do one course in algeria ? alot of people here are interessted in the injection machines
Thank you for the suggestion!! We'll pass it along to our training team! 🙂
I never was a big fan of flash… kind of a wimp, only power he had was speed, but Superman was just as fast if not even faster
Hahaha! And this is why we want to keep him AWAY from our plastic parts! 🤣
Great video. Just wondering why there is 2ejection cycles instead of one?.... lol
My best guess is that it is because the product might not fall of at first ejection :)
We call them cams. Never heard of a slide.
Ahh perfect. Building a machine myself and this was a question ive had that hasnt been well answered or addressed. Thanks
Awesome!! We're so happy it was helpful to you! Thanks for watching!
Too much hold pressure or hold time will cause flash also incorrect shot size and not enough tonnage
So after that semi confusing information you advise to not adjust backpressure? All that nonsense about 'drying the material' via the back pressure setting was just added confusing drivel too. Hygroscopic material needs to bd suitably prepared and conditioned pre moulding, end of. Backpressure is purely an adjustable parameter to ensure consistency in melt preparation. Multiple factors can add inconsistency, wear, polymer, additives and environmental changes. You should use scientific optimisation to determine the ideal backpressure for each and every product you trial/run. Once the process is optimised and passed IQ there is no reason to adjust backpressure (or anything else for that matter) as any defects witnessed at this stage during normal production will stem from an underlying issure that needs revolving NOT by adjusting machine settings. Setters/techs - Dont piss about with machine settings if production was running fine beforehand, examine route cause first. Only once everything has been tripple checked should you consider batch to batch material variation and make minute changes to settings while informing your process engineer.
Andrew, I think we agree on this. We teach a scientific, systematic methodology to find the optimal BP. My stories are there to provide context from my mistakes early in my career. Over my years of instructing, I have found that some people need a direct to the point piece of information and some of us like a story or analogy to drive the point home. Us molders are a tight knit community, we have to pass on what we are learning to the next generation. Thank you for the feed back. - Jason
@rjg I'll be honest Jason, RJG are highly regarded in the UK as a training centre, that's why I watched the video. Are you related (same company)? My comment was almost to distinguish if you were a professional outfit and by your reply, you are. I appreciate you taking the time to reply and it seems we very likely are of the same thoughts. There's many ways to get your point across, I guess for me if you'd explain the optimisation through systematic study first then discussed past wrong doings I may have felt differently, but that's just my opinion, not necessarily the right one.
@@user-mk4nm8yl3u Yes, we are the same company! We have offices around the globe, including the UK. We appreciate you watching and providing feedback! We certainly take it all into consideration. We hope you have a great day!
this video was very informative , didnt know that you had to grease the leader pins . Could you use alchol for an alternative cleaning solution for the mold .
We're so glad you found it helpful! You can use alcohol. The best is to use 80% or higher. Mold cleaner is another option. 🙂
How long does resin needs to dry before going into production.
Thanks for watching! Each material data sheet lists the required drying time and temperature. There is not one standard for all materials. 🙂
Excellent lecture.
We're so happy you enjoyed it, thanks for watching!
Hi sir, background noise disturb a lot.
Thank you for the feedback!! 🙂
Hi there, we are mold maker in Shenzhen China, please contact us if need make injection molds.
Machinery manufacturers like to boost the recovery rates of their machines in terms of oz/second. Therefore they design their screws for maximum recovery. This can lead to unmelted resin, poor mixing with colorants….. Back pressure will certainly help this situation.
I recognise the 1ltr PET bottle 👌👌🤣 hope you're well
Also mold temperature can cause flashing. If the temperature is too high, plastic don't freeze in time.
I just had an issue with HIPS, where I kept getting trapped gas in the barrel, leading to bubbled parts. I increased the back pressure, in an attempt to exhaust the gas through the hopper. I don't have any formal training, so you'll have to excuse me if anything I say is wrong. But, it seems to have worked. I have a ring of splay I'm trying to work out, next. Great video!
Thanks for sharing and for watching!! 😁
I can understand about the explaination on this video. This is simple but a lot of information. Thank you
We're so happy it was helpful! Thank you for watching!!
mould temperature and turbulent water flow is vital, in all injection molding process not just medical, bit surprised RJG say especially medical? learned how important water temperature can be 15 years ago, when trialing a a closure mold on an electric machine, and they had over speced the chiller and temperature of the chiller was varying by 7 degrees ,the melt cushion was trending with it,we ended up removing the chiller and replacing it with water heaters, this reduced the melt cushion variation by 0.6 mm,
If youre shot size is too big
Dry your material!
What kind of clamps are on this mold?
Hi Josh, we bought them from PPE, Plastics Processing Equipment. 🙂
been in processing about 14 years there are so many things and variations that can cause flash.i work with machines from 120 tons to 1100 tons.if youre process is where it is supposed to be to the original than obviously something changed.
I have been working in plastic for over 10 years and started from zero knowledge to working up to supervisor and now learning process more and more each day. I can say everything in this video is well explained and true in every way. These are the exact steps I take to prevent flash in almost every case when you can tell you are overpacking pressure and blowing the tool open. Obviously sometimes it can be from clogged venting and in "some" cases even injection speed can play a huge factor. But at the root of it all, you have to see how much material you are truly trying to push into a tool and where your cut off point needs to be. Your machines are a lot different than mine but also a great point to make is your shot cushion should not be your exact transfer point. There should always be a little "room for pressure" between the sprue break and the injection nozzle as to not cause a bonnet
Thank you so much for your input! We're so happy you enjoyed the video!! ☺
Other cause too much back pressure?
These webinars are really educational and very informative .. Thanks for sharing
We're so happy you enjoy them! Thank you for watching!
What about flashing the gate? Everything you said makes sense for flash on the part.
Holding not working how to check
that was extremely helpful, Thank you for sharing
You're welcome!
hope you release more videos about nissei machine.
Hi, thank you for video. I have a question. If during the injection we do more cooling, semi-crystalline are could increase o no? Cooling can effect more creating semi-crystalline area?
Cooling has an impact on the amount of crystallinity. The faster the cooling ( colder) the less crystal development. Hotter molds allow more time for the crystals to grow. It is important to run the mold at the correct temperature recommended by the material supplier.
Hi and thanks so much for the great topic, I watched your webinar on this topic and it is excellent. I know my question is not that related to this video but I found no better place to ask from you, I'm trying to make a true picture of what the injection machine does and a ask you to clarify this for me if possible, "We know that the driving force in the injection machine is hydralic or electric motor, so when we enter a value for injecion rate or injection velocity in first stage or filling stage what the machine does to maintain the value we set for velocity is it exerts a pressure to see what the resulting velocity is and in a closed loop it sets different pressures to keep the velocity on the value we have entered". What I'm pointing is actually the velocity is a result of a profile of different pressures adjusted by machine to maintain our prefered velocity. Am I correct about this? Thank you.
Thank you for the kind words. On a hydraulic molding machine, there is a pressure limit that is set by the user. This pressure limit allows the machine to use up to that amount to achieve the flow rate. When an injection velocity is set, the hydraulic pump sees this as a certain gallons per minute. The pump will generate that GPM of hydraulic oil. The resistance of moving the screw and the plastic into the mold will start building up a dynamic pressure the further the mold is filled. The pressure limit is established 10-15 % higher than the required pressure under normal circumstances. I hope this clarifies your question.
@@rjg Thanks so much.
Hi and thanks so much for the great topic, I watched your webinar on this topic and it is excellent. I know my question is not that related to this video but I found no better place to ask from you, I'm trying to make a true picture of what the injection machine does and a ask you to clarify this for me if possible, "We know that the driving force in the injection machine is hydralic or electric motor, so when we enter a value for injecion rate or injection velocity in first stage or filling stage what the machine does to maintain the value we set for velocity is it exerts a pressure to see what the resulting velocity is and in a closed loop it sets different pressures to keep the velocity on the value we have entered". What I'm pointing is actually the velocity is a result of a profile of different pressures adjusted by machine to maintain our prefered velocity. Am I correct about this? Thank you.
I have to ask because I have been looking to purchase a few platen stones for the plant I work in but I am having a difficult time finding where to purchase them. Any suggestions?
Example LSR injection , the solidify temperature is around 140 degree Celsius. Should use pressurised water for better uniform surface temperature?
Thank you sir!
You are welcome!
That last tip on the bolt is something I stress so much to mold setters.
SO important! Sounds like they have a great teacher!
@@rjgwhat if we found something wrong when bolt usage, what we do then ?
I always say 1-1/2 - 2x nothing less nothing more. Also the importance of bolt to heel ratio on clamps and heel thickness.. when I got to my place there was only one mold setter and he was only gunning the bolts in about 2/3rd of the thickness and he was sliding the clamps as far in as he can and not really paying attention to the thickness of the heel (always want it slightly more then the plate) and I had to explain that it's like a teeter totter and theirs not as much leverage that way. I'd take a clamp that's 2" on the plate over one that's 4" on the plate any day that way the distribution is more evenly and not just on the heel.
that is unless if the platen holes are reallllly close to the plate like within 2 inches but 3-4 inches away just throw an extra on each side and use the toe even if it's on the flat side.